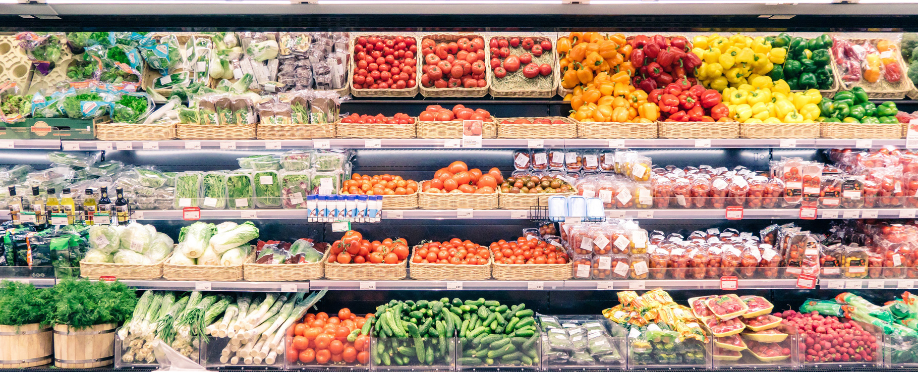
From keeping up with the latest consumer expectations to managing net zero legislation standards, grocery retailers have enough challenges as it is threatening their profitability to let grocery shrink cut significantly into their bottom line. This makes shrink reduction increasingly critical for facilities managers in the grocery space. Keep reading to learn some of the most cutting-edge shrink reduction strategies in use among today’s top retailers.
What is shrink reduction?
Shrink reduction is the act of preventing the loss of product. Causes of shrinkage in retail stores can include administrative errors, fraud, shoplifting, employee theft, and food going bad. In this article, we’ll be tackling the subject of food waste in particular.
There are several main causes behind grocery shrink, including power outages, unexpected equipment downtime, refrigeration issues, and insufficient maintenance, among other reasons, but luckily it can be corrected with some basic best practices.
And, as George Campbell, head of technical services at City US, can attest, the ROI makes it well worth investing in these shrink-reducing strategies “When you consider that grocery stores lose as much as over three percent of total sales each year to shrink,” he said, “even if you can reduce that by as little as 10%, the savings can be enormous.”
Shrink reduction strategies
Here are some ways grocery facilities managers can minimize shrink:
1. Regular preventative maintenance
The prevention of grocery shrink largely hinges on the condition of refrigeration and other equipment. This makes creating and executing a preventative maintenance plan focused on increasing asset uptime an important foundation for any shrink reduction program.
Start with a priority-driven plan that stresses regular case cleaning, mister system maintenance, and other critical maintenance tasks for boosting the efficiency of equipment that keeps products fresh. In particular, facilities managers increasingly recognize the importance of regular case cleaning, which involves:
- Cleaning condenser coils and evaporators
- Ensuring proper drainage at the bottom of cases
- Preventing water leaks
- Vacuuming and cleaning out old product
2. Ultrasound predictive maintenance technology
Just like preventative maintenance plans, predictive maintenance is all about avoiding issues before they begin — but in this case, specialized tools are used to monitor the performance of equipment to detect issues early on before they lead to system failure (and shrink-causing downtime).
Various predictive maintenance tools abound, including ultrasound technology, infrared analysis, vibration analysis, laser-shaft alignment, oil analysis, and the use of AI and machine learning in predictive analytics.
At City, Campbell has spearheaded the use of SOUNDTech+ ultrasound technology, the City branded predictive maintenance tool powered by DST, for refrigeration equipment. A seasoned hands-on technician himself, he was astonished at the results of City’s 10-month pilot program, in which SOUNDTech+ prevented catastrophic refrigeration failure before the issue became a problem — with 98% accuracy.
Campbell predicts that ultrasound predictive maintenance technology, used in tandem with a preventative maintenance schedule, will become a major asset for grocery retailers seeking to prevent product loss.
3. Remote monitoring
With remote energy monitoring, equipment sensors are connected to computerized maintenance management systems (CMMS) and energy management systems (EMS). By generating instant alerts, spotting patterns, and automatically issuing work orders when repairs are needed, this has become a vital strategy for remotely monitoring and controlling energy consumption of units such as refrigeration, hot bars, and other food and beverage equipment.
For example, City has developed a robust analytics platform that sits on top of EMS systems and targets anomalies in asset specification or energy consumption at partner sites. If temperatures spike or fall outside their expected range, the program sends alerts to facilities managers who can investigate and address issues before food spoils, avoiding costly grocery shrink and equipment repairs. In some cases, problems can even be fixed remotely.
Additionally, AI tools can be used to monitor refrigeration temperatures and performance at the case level, preventing grocery shrink and assigning preventative maintenance tasks to field resources.
4. Expert refrigeration management
Thanks to rapidly evolving technologies and increasingly rigorous sustainability standards, refrigeration management has become a fast-paced field requiring constant learning and development. This makes continued training for in-house technicians and hiring experienced facilities management providers an essential part of any grocery shrink reduction program.
A facilities management company well-versed in refrigeration management can recommend technologies, integrate new systems for monitoring equipment performance and predicting issues, and create a strategic roadmap for adopting refrigeration management best practices.
A good FM partner can support you by giving you a good understanding of your assets. We’re your eyes and ears and boots on the groundTony Parkinson
“A good FM partner can support you by giving you a good understanding of your assets. We’re your eyes and ears and boots on the ground,” said Tony Parkinson, senior vice president of West Coast operations at City.
With an integrated facilities management partner, all facility operations and processes are fulfilled holistically through a single third-party managed provider. Thanks to stronger accountability and streamlined processes, this end-to-end support can improve efficiencies and communication, leading to an overall enhanced experience reflected in lower grocery shrink among other tangible benefits.