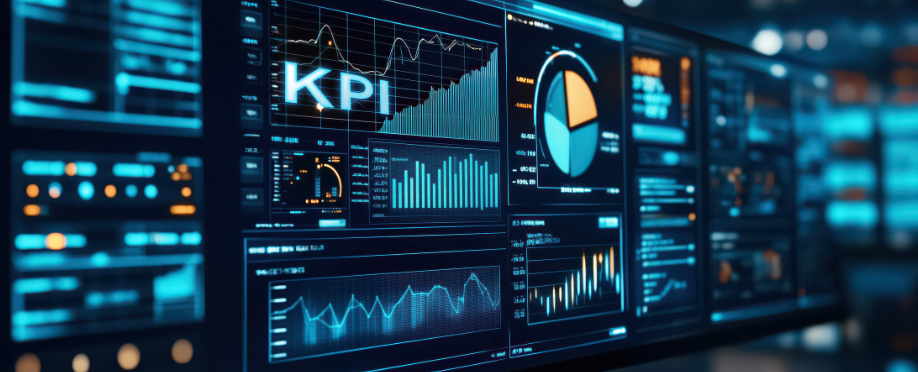
In today’s fast-paced retail environment, equipment failures and downtime can be costly — especially in the form of both lost sales and spoiled inventory. In fact, unplanned downtime costs has historically averaged $5,600 a minute across all industries, with recent studies putting this figure as high as $9,000 a minute.
The good news? Facilities management leaders can stay ahead of these losses by tracking key maintenance KPIs (key performance indicators) — metrics that reveal how well operations are keeping stores up and running. By focusing on the right metrics, retail facilities teams can increase equipment uptime, reduce costs, and improve service quality, all in support of broader facilities management goals.
In this article, we’ll explore what maintenance KPIs are (and how they differ from other facilities metrics), highlight the most important maintenance KPIs for retail facilities, and share best practices for building a data-driven maintenance culture.
What Are Maintenance KPIs?
Maintenance KPIs are specific metrics that help facilities and maintenance teams evaluate how effectively their maintenance operations are running. From the speed of repairs to how often problems are resolved right the first time, such insights reveal the efficiency, effectiveness, and quality of maintenance activities.
Maintenance KPIs answer questions like:
- How fast and effectively can your team address equipment problems?
- How well do your team’s maintenance efforts prevent issues?
- Is your organization prioritizing the right types of maintenance — e.g., reactive vs. preventive?
It’s important to distinguish maintenance KPIs from asset-level or energy KPIs. Whereas maintenance-focused metrics evaluate maintenance processes and team performance, asset reliability KPIs like Mean Time Between Failures (MTBF) measure how long equipment runs before failing. This is a useful figure for engineering and reliability, but not a direct indicator of your repair team’s speed or service quality.
Similarly, financial metrics like Maintenance Cost as a Percent of Replacement Asset Value (RAV) help assess how your maintenance spend aligns with the overall value of your assets — but they don’t speak to day-to-day team efficiency or operational uptime.
Similarly, energy KPIs track things like energy consumption or efficiency improvements — valuable for ET&S (energy transition and sustainability) reporting but outside the scope of maintenance team evaluation.
Key Maintenance KPIs to Track
When it comes to retail facilities like grocery, convenience, and other food retail, there are a handful of maintenance KPIs that stand out as especially critical. These core KPIs can be grouped into four categories:
- Repair Efficiency: How quickly and efficiently are repairs completed? (e.g., Mean Time To Repair and First Time Fix Rate)
- Uptime/Downtime: How well are you avoiding downtime? (e.g., uptime percentage of critical equipment)
- Service Satisfaction: How satisfied are stakeholders with maintenance service? (e.g., quality of service ratings or repeat issue rates)
- Preventive Maintenance (PM) Program Performance: How effective is our PM program in balancing proactive vs. reactive work? (e.g., Planned Maintenance Percentage)
Measuring Repair Efficiency
1. Mean Time To Repair (MTTR)
What it means
MTTR measures how quickly your team can diagnose and fix issues, typically expressed in hours.
How to calculate it
Divide the total repair time by the number of repairs.
MTTR = Total Repair Time ➗ Number of Repairs
For example, if technicians spent 40 hours to complete 10 repairs, the average MTTR would be 4 hours per repair.
What to know about it
A lower MTTR means equipment is restored faster, minimizing downtime.
In practice, retail FM teams will set benchmark targets for MTTR — for instance, resolving urgent issues within 4 hours on average — and use real-time reporting to track if they’re hitting that mark.
MTTR can vary by asset criticality — fixing a refrigeration rack might naturally take longer than replacing a light ballast, for example — but tracking it helps identify bottlenecks.
A high MTTR could indicate delays in troubleshooting, lack of spare parts, or insufficient technician training. In grocery and food retail, keeping MTTR low is vital because every hour of refrigeration or HVAC downtime risks product loss and customer discomfort or dissatisfaction.
2. First Time Fix Rate (FTFR)
What it means
While MTTR looks at speed, FTFR measures repair effectiveness — specifically, the percentage of work orders resolved on the first visit and without requiring a repeat visit.
How to calculate it
Take the number of issues fixed on the initial attempt divided by the total number of issues, and multiply by 100 to establish a percentage.
FTFR (%) = (First Time Fixes ➗ Total Service Calls) × 100
For example, an FTFR of 85% means 85 out of 100 service calls are fixed in one go, with no callbacks needed.
What to know about it
A low First Time Fix Rate can wreak havoc on schedules and budgets. Repeat visits mean longer downtime, higher labor costs, and frustration for store staff waiting on repairs.
To improve FTFR, ensure technicians are well-trained to deliver accurate diagnoses and properly equipped with the right inventory and tools, recommends Cristee Monahan, Vice-President of Central Operations at City Facilities Management.
“With some basic upfront data from technicians, AI-powered systems can make impressively accurate parts recommendations,” adds Cristee. “This drastically cuts down on repeat site visits and helps get units back up faster.”
This drastically cuts down on repeat site visits and helps get units back up faster.Cristee Monahan, VP of Central Operations
Retailers should benchmark their FTFR and implement processes to inch it higher; even a 5–10% improvement can significantly reduce total maintenance visits and downtime.
Measuring Uptime/Downtime
3. Equipment Uptime Percentage
What it means
Uptime is a broad KPI that encapsulates the impact of all your maintenance efforts, both preventive and reactive. The flipside of downtime, it represents the percentage of time that critical equipment is operational and available.
How to calculate it
Take the total time minus downtime, divide by the total time, and multiply by 100 to calculate the percentage of time equipment is operational.
Uptime (%)=((Total Time − Downtime) ➗ Total Time) × 100
For example, if a store’s refrigeration units were functional 98 out of 100 hours, the uptime would be 98%.
What to know about it
“Whether you choose to track uptime or downtime is entirely up to the organization — as they both express the same operational reality,” says Cristee.
Many facilities teams strive for “four nines” (99.99%) in IT systems, but for physical store equipment, a realistic uptime target might be 95–99% depending on the asset.
High uptime means fewer disruptions to store operations — refrigerators stay cold, ovens stay hot, and checkout systems stay online — directly protecting revenue.
Even a few hours of refrigeration downtime can cost thousands in lost sales and spoiled food, making tracking and maximizing uptime a top priority in retail store facilities management.
Measuring Service Satisfaction
4. Service Satisfaction
What it means
Maintenance performance isn’t only about technical stats; it’s also about customer service. In facilities management for retail, “customers” in this realm are often store managers, employees, or even shoppers who experience the store environment and therefore are affected by maintenance service.
Service Satisfaction, which gauges how happy these stakeholders are with the maintenance service provided, is known as “soft” KPI in that it reflects subjective perceptions rather than so-called “hard” data like repair time or uptime.
How to calculate it
This can be measured through surveys or feedback scores. For instance, after a work order is closed, the store manager may rate the service on timeliness, communication, and effectiveness.
Service satisfaction can also be inferred indirectly via metrics like percentage of repeat issues (if an issue has to be fixed multiple times, satisfaction likely suffers) or response time vs. SLA target.
What to know about it
High service satisfaction means fewer complaints about facilities issues and a better reputation for the FM team.
What’s more, a store manager who trusts the maintenance team will be more proactive in reporting issues early, which in turn helps the whole organization run better.
This KPI also can also correlate with compliance. If maintenance problems are fixed promptly, stores are more likely up to standards for safety and compliance, improving overall morale.
Measuring Preventive Maintenance Program Performance
5. Planned Maintenance Percentage (PMP)
What it means
A strong PM program reduces emergency fixes and extends asset life — but how do you measure it? The go-to KPI is Planned Maintenance Percentage (PMP). PMP represents the proportion of maintenance work that is planned (or scheduled) versus unplanned.
How to calculate it
To get the percentage of time spent on planned maintenance, take the planned maintenance hours, divide by the total maintenance hours, and multiply by 100.
PMP(%) = (Planned maintenance hours ➗ Total maintenance hours) × 100
For instance, if your team spent 300 hours last month on maintenance, and 240 of those hours were spent executing scheduled PM tasks (with 60 hours on reactive repairs), your PMP is 80%.
What to know about it
The higher the PMP the better, as it indicates that you’re dedicating most of your time to planned inspections, routine servicing, and other preventive activities instead of constantly fighting fires.
According to industry best practices, world-class maintenance organizations should aim for ~85% or higher PMP. In retail, hitting that number can be challenging if you have older assets or insufficient staffing, but it’s a useful benchmark. At City, Cristee says, the team aims for 99%.
Maintenance KPIs Best Practices
Tracking metrics is one thing; using them to drive improvement is another. To truly benefit from maintenance KPIs, retail facilities leaders should foster a culture and environment that leverages data for real-time decision-making and continuous progress.
Here are some of Cristee’s go-to best practices to get the most out of your maintenance KPIs:
1. Utilize Real-Time Reporting and Dashboards
Don’t let KPIs gather dust in a monthly report. Use a computerized maintenance management system (CMMS) or integrated platform to track metrics like MTTR, FTFR, and PMP in real time.
Live dashboards can highlight when a KPI is slipping (e.g., a spike in open work orders or rising downtime hours), allowing facilities teams to act quickly. Instant alerts and mobile access to KPI data also help ensure issues are spotted early, aligning with City’s motto “City Sees It First,” which underscores the value the City team places on proactive awareness.
2. Optimize Your Tech Stack
Embrace the right technology that supports your KPI goals. This typically includes IoT sensors and remote monitoring to catch equipment anomalies — improving uptime by fixing issues before failure. Or AI-driven work order dispatching to match the best technician for each job, improving FTFR. Even simple tools like digital checklists can ensure PM tasks are completed on time and support your PMP targets.
City, for example, utilizes predictive tools like SOUNDTech+ to detect equipment issues before breakdowns, as well as AI parts prediction to reduce repeat visits. Having an integrated intelligence and automation capabilities not only makes maintenance work smarter and faster, it also feeds better data back into your KPIs.
3. Cultivate a KPI-Focused Culture
Make KPIs part of the daily language for your maintenance team. Technicians and facility managers should understand why each KPI matters and how their actions influence the numbers.
Encourage ownership by sharing KPI results regularly — for example during weekly huddles.
When team members know the importance of First Time Fix Rates, they’re more likely to take those extra steps (like double-checking they have the right parts or information before dispatch) to hit the target.
Celebrate improvements in KPIs and when numbers dip, focus on what can be learned. When the culture treats KPIs as tools for progress, not pressure, real performance gains follow.
Beyond Maintenance Service: Other Facilities Management KPIs
Maintenance KPIs are a core piece of facilities management performance, but they’re not the whole picture. In an integrated model, all these KPIs work together to paint a full picture of facility health.
Here’s a quick look at areas beyond maintenance service and the kinds of KPIs you might monitor in each:
Asset Management KPIs
Asset management metrics evaluate the lifecycle and cost-effectiveness of physical assets. Examples include:
- Maintenance Cost Per Asset
- Asset Uptime Percentage (a maintenance metric but at the asset level)
- Capital Expenditure vs. Operating Expenditure Ratios
- Replacement planning metrics like the age profile of equipment
One important asset KPI in maintenance strategy is maintenance cost as a percentage of RAV (Replacement Asset Value). This indicates if you’re over-investing in repairs relative to what an asset is worth. A rule of thumb is to consider replacing an asset when annual maintenance costs exceed, say, 50% of its RAV.
Energy Management KPIs
Energy is one of the highest costs for grocery and food retailers, and refrigeration alone is notoriously energy-intensive. Common KPIs here include:
- Energy Consumption Per Square Foot
- HVAC/refrigeration energy efficiency ratings
- Carbon footprint or emissions metrics
Tracking energy management helps retailers meet sustainability targets and reduce utility expenses. Strong maintenance practices, such as cleaning condensers, inevitably boost energy KPIs.
Safety and Compliance KPIs
Safety is paramount in food retail facilities. KPIs in this realm might include:
- The number of safety incidents or accidents
- Compliance audit scores
- Inspection completion rates
These metrics tie closely with maintenance too. After all, a well-maintained store is a safer store. Consider implementing a grocery store safety checklist program and tracking compliance with the checklist as a KPI. High safety metrics protect employees, customers, and the company’s reputation while minimizing legal risks.
HR/Workforce KPIs
Given the shortage of skilled tradespeople, managing your maintenance workforce is critical. KPIs here include:
- Technician Retention Rate
- Training Hours Completed
- Work Orders Completed Per Technician Per Day (otherwise known as Efficiency)
Some organizations also track employee satisfaction within the facilities team as a KPI, understanding that engaged employees tend to deliver better service.
High turnover or low training investment can warn of future maintenance performance issues. Conversely, strong development programs (like hands-on training initiatives) can boost productivity and service quality.
Translating Maintenance KPIs into Action
Tracking the right maintenance KPIs — from repair speed and first-time fix rate to equipment uptime, service satisfaction, and proactive maintenance levels — gives facilities leaders the power to make informed decisions and continuously improve operations.
Remember that metrics are a means to an end. The ultimate goal is to provide safe, efficient, and reliable store environments that support great customer experiences and profitable sales.
As part of our industry-disruptive, data-driven facilities management system for grocery stores, convenience stores, and other retailers, City works with FM teams to implement the latest and most innovative practices that improve service quality, reduce costs, and meet sustainability targets.
Learn more about our intelligence solutions to elevate your facilities management program and start turning maintenance KPIs into continuous improvement drivers for your retail operations.