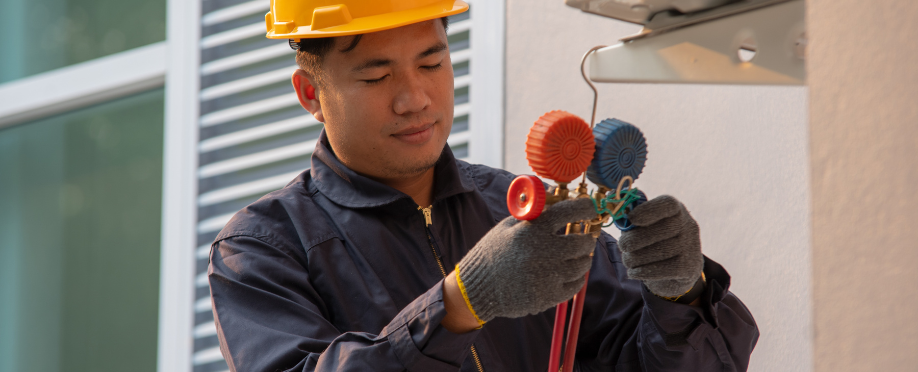
What if there was one simple shift you could make in your facilities strategy that would reduce costs, extend asset life, and improve customer satisfaction? For many FM leaders, understanding the difference between reactive vs. preventive maintenance can be the game-changing move that transforms their operations.
In facilities management, maintenance can be said to fall into four main categories. While all of them have their place in an FM strategy, failure to maintain a proper balance by leaning too hard on reactive maintenance can be detrimental to a retail business. In addition to reducing operational capacity, it can result in higher maintenance costs, lower employee retention, higher incidence of equipment downtime, shorter asset life, and customer experience issues.
Today we’ll cover preventive maintenance vs. reactive maintenance, explore the four types of maintenance in depth, and offer some insights into how FM leaders can take a more proactive approach to facilities management.
What is preventive maintenance?
Reactive maintenance vs. preventive maintenance
Preventive maintenance vs. predictive maintenance
What is reactive maintenance?
Reactive maintenance meaning
A reactive maintenance approach means just that — reacting to issues or breakdowns after they happen. When equipment breaks down, a service technician will diagnose the issue and then take the proper steps to repair the machine. While reactive maintenance is a vital part of an FM strategy, as equipment does break down over time even with strong PM programs, operating fully on a “run it ‘til it breaks” mentality inevitably leads to higher costs down the road as well as higher stress levels.
What are the disadvantages of reactive maintenance?
“One of the main problems with reactive maintenance is that it’s something of a universal rule that unexpected breakdowns occur at the least convenient times,” says George Campbell, who oversees service delivery for City as Director of Technical Services. This can lead to overwhelmed technicians, overtime hours, as well as costly emergency service calls.
A culture of reactive maintenance can contribute to deferred maintenance and lead to other costly consequences, such as:
- Frequent and unexpected equipment breakdowns due to lack of regular preventive maintenance
- Service delays
- Food product loss
- Lower customer satisfaction
What is preventive maintenance?
Preventive maintenance is a proactive approach to facilities management, which involves regular inspection, detection, prevention, and correction before issues become serious problems and result in breakdowns. Assets are monitored in real time and predictive technology is used to identify mechanical issues and discrepancies, and steps are taken to make corrections.
Why is PM better than reactive maintenance?
A solid preventive maintenance program is better than reactive maintenance because it brings higher equipment uptime and lower costs, making it one of the key facilities management best practices. Other benefits include:
- Increasing the lifespan and productivity of assets
- Minimizing equipment depreciation
- Increasing efficiency of facilities management workflows
- Reducing emergency maintenance costs
- Enhancing work-life balance with fewer overtime and weekend hours (thereby increasing employee retention)
- Higher customer satisfaction and loyalty
To get started on or strengthen a preventative maintenance program, check out our guide on preventive maintenance checklists.
Reactive maintenance vs. preventive maintenance
The two main approaches to facilities management are reactive maintenance and preventive maintenance.
What is the difference between reactive and preventive maintenance? Reactive maintenance is a necessary part of the job, as unplanned issues and breakdowns will inevitably occur even with solid preventive measures in place. Preventive maintenance, on the other hand, has as its goal addressing issues before they turn into problems that lead to equipment downtime and unexpected service calls.
You could say George’s mission is to make preventive maintenance the dominant approach to facilities management. “The preventive world has been overlooked for too long,” he says. “But if you spend the time today to prevent the time you’ll spend tomorrow when equipment breaks down unexpectedly, you’ll actually end up saving more time, and of course, money.” He adds that 30 percent of food in U.S. grocery stores is thrown away, amounting to 16 billion pounds of food waste every year.
“While it might appear that reactive maintenance saves money and time compared to a preventative approach, in the end you’ll end up spending more on service calls, replacing parts, and shorter asset life spans,” George says.
Preventive vs. preventative maintenance
Is it preventive maintenance or preventative maintenance? While both “preventive” and “preventative” are technically correct, “preventive maintenance” is generally the preferred term in the facilities management field. It refers to scheduled upkeep designed to prevent breakdowns, reduce downtime, and extend the life of equipment — a proactive alternative to reactive maintenance. |
Preventive maintenance vs. predictive maintenance
Predictive maintenance falls under preventive maintenance and can be defined as the use of predictive technology to detect mechanical issues before they result in failure.
A number of different predictive maintenance technologies exist, including ultrasound technology, vibration analysis infrared analysis, and predictive analytics using AI and machine learning. George utilizes SOUNDTech+ ultrasound technology, the City branded predictive maintenance tool powered by DST, which has a track record in the field of predicting catastrophic refrigeration rack failure before it becomes an issue with up to 98% accuracy once the tool is programmed.
“This technology is going to change everything,” George says. “It makes technicians’ jobs much easier and faster, especially newer technicians who don’t have as much experience in the field.”
[The SOUNDTech+ tool] makes technicians’ jobs much easier and faster.George Campbell, Director of Technical Services at City
The benefits of predictive maintenance include:
- Precise diagnostics
- Shorter service calls
- Fewer emergency maintenance calls
- Less downtime
- Less shrink
- More informed capital planning and forecasting
Corrective maintenance
Even with a rigorous PM program and the most cutting-edge predictive technology, over time equipment loses efficiency. This is where corrective maintenance comes in.
Preventive and corrective maintenance
Sometimes used interchangeably with preventive maintenance, corrective maintenance actually refers to maintenance tasks and repairs that are performed to restore equipment to peak efficiency.
In the grocery industry, recommissioning is usually performed every three to five years in order to correct issues and restore efficiency. However, as George points out, thanks to predictive technology, facilities managers can take steps on a continual basis to ensure equipment is in good working order instead of letting issues build up over time. This means fewer breakdowns, higher efficiency, and less frequent recommissioning.
A Proactive Approach to Facilities Management
In today’s market, it’s more important than ever for facilities management leaders to manage costs, maintain employee satisfaction, and maintain efficiencies. While a paradigm shift from reactive maintenance to a preventive approach can be a massive undertaking, it’s critical for staying competitive.
At City, we offer an industry-disruptive delivery system for facilities management founded on preventive maintenance that can help your business make the leap. Learn more about our Integrated Facilities Management services.