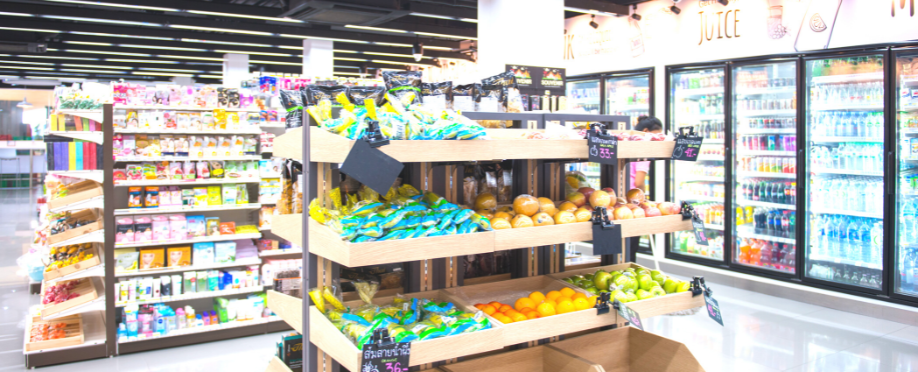
With the global pandemic largely behind us, grocers are now faced with a new challenge — the acceleration of sustainability initiatives fueled by new international agreements and state and national laws regulating greenhouse gas emissions.
“…[Sustainability] is increasingly a strategic differentiating factor for retailers and a source of value and growth in often challenging, stagnating market environments,” McKinsey notes in a recent report.
One of the most effective ways grocers can reduce emissions on their path to a greener future is by implementing sustainable grocery store design, for both new stores as well as existing facilities.
We spoke with Cary Nix, Senior VP of Engineering and Operations, and John Pulley, VP of MEP Services, for CBES (City Building and Engineering Services) about how to create an energy-efficient grocery store design that will meet the demands of stricter regulations as well as an increasingly eco-conscious customer base.
Between them, Cary and John have 55 years of building and construction experience in the grocery store industry. Here are some of the sustainability best practices they see grocers overlook most often when it comes to grocery store design.
Sustainable Grocery Store Design Best Practices
While developing MEP plans is one of the latter steps in a remodel or construction project, it’s vital for facilities leaders, planners, and architects to have a solid grasp of MEP/R (Mechanical, Electrical, Plumbing, and Refrigeration) best practices for sustainable grocery store design from the very start of a project. This will help streamline the design and construction process as well as ensure a proper budget is in place for the sustainable design.
Here are some of the most commonly neglected best practices for energy-efficient supermarket design. When implemented, they can help grocery stores bring their existing facilities up to standard and put them on track to meet net zero goals.
1. Replace old or inefficient equipment
One of the most overlooked sustainable practices when renovating stores is failing to eliminate old equipment that has reached or exceeded its serviceable life.
At a certain point, it actually costs more to run equipment than to just replace it.John Pulley. VP of MEP Services at CBES
“At a certain point,” John explains, “it actually costs more to run equipment than to just replace it.”
Even newer equipment, while still in working condition, may be poorly designed for energy efficiency. For example, Cary says, “replacing an open multideck refrigeration case with a reach-in multi-deck case outfitted with doors can reduce energy consumption by as much as 50 percent for that unit.”
Such equipment upgrades are often missed due to the budget allotment, which fails to account for replacing such items. Fortunately, Cary finds that given the increased emphasis on energy management these days, grocers are increasingly open to outfitting renovated facilities with new, energy-efficient assets as long as they’re properly budgeted for.
2. Perform due diligence with major structural changes
One thing that’s easily missed on fixture plans occurs with major structural changes is taking down a wall that contains electrical panels and refrigeration piping. “You’d be surprised how often issues occur from not investigating whether utilities are housed within a wall slated for demolition,” John says.
“Even engineers can overlook this issue when putting together the MEP/R plans,” he goes on to say. “But it’s a costly one to miss. Performing thorough investigations as part of due diligence surveys can help ensure MEP engineers do a deep dive into the areas affected by the renovations.”
3. Address deferred maintenance issues
Deferred maintenance is another step that’s often missed as part of the renovation process — that is, maintenance or repairs to the facility and assets that get backlogged, generally due to resource or budgetary constraints.
“It’s not uncommon when doing a remodel for grocers to pay more attention to customer-facing items, which can result in maintenance cuts from the budget,” Cary explains. “However, while taking care of major equipment repairs may not provide an obvious sales bump, if you keep kicking the can down the road, you may end up incurring even higher costs when equipment needs to be replaced prematurely.”
Cary also points out that avoiding needed repairs can even reduce sales by impacting the customer experience. “With leaking refrigerated cases, you end up with wet floors and slip and fall risks. Refrigeration issues can also impact product freshness or lead to stockouts when unexpected breakdowns occur.”
4. Commissioning
Commissioning is a QA procedure that ensures equipment and assets operate as they were intended by the manufacturer so they can function at optimal efficiency. By getting the set points, pressurization, and other factors just right, a store can minimize energy consumption and optimize performance, which leads to lower energy costs, lower maintenance costs, and longer equipment life, not to mention reduction of greenhouse gas emissions.
“You could have the best design in the world,” John says, “But if your equipment isn’t maintained correctly, you’re not going to properly operate on the equipment efficiently. This is why John recommends commissioning of new equipment with every remodel and new store build, plus regular equipment monitoring to ensure assets continue to operate at their highest levels.
Sustainable Grocery Store Design, Building, and Engineering Services
Facilities leaders have a lot to think about as they navigate the path to net zero emissions. Choosing an experienced professional services partner well-versed in creative sustainability solutions is critical to meeting decarbonization commitments, lowering energy consumption and costs, and optimizing customers’ shopping experience.
CBES features an integrated engineering, construction, program management, and energy management team that offers end-to-end system analysis of new and existing MEP/R systems with the goal of minimizing energy usage, operating expenses, and environmental impact. Learn more about our design, building, and engineering services.